Aluminum alloy extruded profiles are characterized by good plasticity, light weight, corrosion resistance, high specific strength (2, 6, and 7 series aluminum alloy materials can be aging strengthened to obtain higher strength) and surface treatment. A large number of curved parts are used to make various curved parts, which are widely used in rail transit vehicles, aerospace equipment, logistics conveyor rail frames, automobile ship skeletons, building curtain wall structural parts, medical equipment rails, home decoration and many other fields. The design requirements of curved parts are also diversified and functional. With the continuous improvement of science and technology and process equipment, the bending process is also diversified. Foreign curved technology has a history of 30 to 40 years of development, and strong technical force. However, the development and manufacture of high-end products in China is limited to large-scale enterprises such as rail vehicle profile plants and aerospace manufacturing plants. The technology monopoly is strong, and the overall strength of domestic bending forming manufacturing technology is significantly different than that of foreign countries.
The profile bending process can be divided into: bending and forming (two-dimensional, three-dimensional), roll forming, press forming, and bending forming according to the different bending process and bending process principle. According to the shape of the workpiece, it can be divided into two-dimensional curved workpiece (see Figure 1) and three-dimensional curved workpiece (see Figure 2).
In the following, the bending process is classified according to the curved device and the curved process principle.
1. Drawing and bending process
(1) Working principle of drawing and bending (two-dimensional) The bending process is basically divided into three steps: In the first step, the equipment stretching cylinder jaw clamps the material and applies a pre-stretching force to the profile to reach the material yield strength. In the second step, the bending cylinder of the bending machine is loaded with bending and rotating, and the stretching cylinder sets the axial pulling force according to the program, so that the profile is made to fit around the bending and bending mold to form the material. In the third step, the tension is increased according to the deformation of the material deformation (the structure of the bending device is shown in Figure 3). During the bending and forming process, while the workpiece is being bent, the stretching cylinder always applies an axial pulling force to the workpiece. The elongation of the material length is always compensated by the stretching cylinder, which avoids the wrinkling tendency of the material and can obtain good performance. Radian effect.
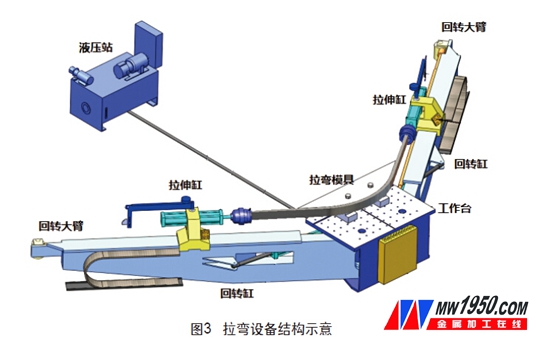
(2) Features of the bending and forming process Advantages: 1 It is capable of drawing and forming a profile section with complicated structure. 2 It can realize profile bending and forming of multi-arc variable curvature. 3 The bending precision is high, the material rebound is stable, and the consistency of the workpiece size is good. 4 can effectively eliminate the residual stress inside the material, and the product dimensional stability is good. 5 Due to the cold work hardening of the metal material, the mechanical properties of the material can be improved after the material is bent. Process defects: 1 The size of the section of the product is limited by the tonnage of the equipment and the size of the jaws. 2 The cost of inputting the bending die is large, and the versatility of the mold is poor. 3 For the asymmetrical section of the profile, it is difficult to control the section deformation of the bent part.
(3) Key technology of the bending and forming process The arc design principle of the bending and bending workpiece is not limited to the elongation of the material. In the bending and forming process, forming defects such as thinning and fracture of the profile wall, wrinkles, and cross-section distortion will occur. The forming defects are closely related to the mechanical properties, section shape and bending process parameters of the profile.
During the bending process, the stress state of each part of the material deformation zone is different. The material outside the neutral layer is subjected to tensile stress, and the material inside the neutral zone (fitting with the bending die) is subjected to compressive stress, so that the material is not subjected to compressive stress. The wrinkling phenomenon occurs, and the pre-stretching force is sufficient to cause the material to yield and stretch, and the metal other than the corresponding neutral layer will be subjected to a larger tensile force, and the wall thickness is reduced and the fracture tends to occur. Therefore, how to balance the material does not wrinkle and the metal outside the neutral layer does not break, and avoid the deformation of the section size of the profile is too large, which is the two key considerations for determining the parameters of the bending process.
(4) Calculation of forming force of stretched profile In the technical capability review of the project, three factors need to be considered: whether the jaw distance of the equipment satisfies the tensile length of the material, whether the jaw size satisfies the section size clamping requirement, and The most critical point in the forming of the bend is to calculate the maximum amount of tensile force required for the material. The forming capacity of the workpiece is calculated and the yield strength value is calculated as 1.25 times the safety factor to ensure that the equipment does not work under the maximum tensile load. The maximum tensile force of the equipment is greater than the required tensile force of the material calculated by the formula, indicating that the tensile capacity of the equipment meets the material. Pulling force requirements.
(5) Three-dimensional bending machine and three-dimensional bending and bending technology The main frame of the three-dimensional bending and bending equipment consists of a welded body frame structure installed on the foundation, as shown in Figure 4, the main frame is used to support the rotatable stretching rocker arm. 2 and hydraulic cylinders. A work platform 1 on which the mold can be placed is mounted on the top of the rack. Two stretching cylinder brackets 9 are respectively mounted on the upper portion of the rocker arm 2, and are electrically positioned by electrically driving the spiral guide rods to accommodate workpieces of different lengths. A stretching cylinder 4 is provided on each of the rocker arms 2. The distortion of the part is carried out by a hydraulic motor 7 with a gearbox mounted behind the stretching cylinder 4. The stretching cylinder 4 is mounted on the bracket 9 by a universal joint which allows the jaws of the clamp 8 to freely rotate forward or backward. The clamp lifting cylinder 5 realizes the gradual lifting of the stretching cylinder 4 during the stretching process, and the clamping pitch cylinder 6 can make the stretching cylinder 4 up and down, and all the movements of the moving pair on the bracket 9 (stretching-lifting-tilting) - Rotating) The workpiece is subjected to tangential stretching along the surface of the three-dimensional mold during the entire forming process to form a three-dimensional three-dimensional workpiece.
Equipment structure and equipment working principle: The key technology of 3D bending is mainly mold design. The 3D bending machine will not give the ideal 3D bending process. The process designer needs to analyze the system according to the performance and bending of the material or CAE limited. Meta-analysis, through continuous trial production of workpieces, to achieve the best match between the three-dimensional bending mold and the three-dimensional bending process, and to meet the technical requirements of the workpiece, requires the process technicians to have a high product development capability.
Space three-dimensional workpieces have many applications in high-speed train front structural parts and aircraft manufacturing. The product has high technical content, large mold input cost, long development cycle, and high added value of products. Fig. 5 and Fig. 6 are typical examples of forming a workpiece by a bending and bending process.
2. Roll forming process
(1) Working principle of roll forming The roll bending machine is generally divided into a vertical roll bending machine and a horizontal roll bending machine, as shown in Figs. 7 and 8. Vertical roll bending machine is easy to load, and horizontal type should be used for long workpieces, as shown in Figure 9. The process position of each axis of the roll bending machine is precisely controlled by the servo motor. The hydraulic motor system drives the linkage of each axis, and the servo motor is controlled by the programmable controller (PLC). While the equipment roller shaft bends the workpiece, the encoder on the equipment monitors the arc length of the workpiece roll in real time and feeds the data to the feedback system. The device performs multiple reciprocating roll bending or multi-radius roll bending according to the setting program. motion.
(2) Roll Bending Forming Process Features Roller bending machines are generally used for the production of single arc workpieces. The mold making cycle is short, the input cost is low, and the operation is simple. For multi-arc workpieces, the CNC roll bending machine can realize the multi-curve bending requirements of the workpiece. However, due to the difference in material hardness of the aluminum profile itself, the deformation degree of each arc segment of the workpiece is different, the rebound is uneven, and the workpiece shape during production. The consistency is not good and requires manual correction. The roll bending process is suitable for the production of large-volume single-arc workpieces or small-volume multi-arc workpieces.
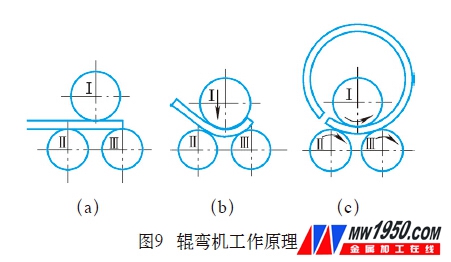
(3) Key technology of roll forming process The difficulty of roll bending process depends on the cross-sectional shape of the curved material. Roller die design is the key to the forming technology of the workpiece. Generally, the mold material is selected from 45 quenched steel or die steel by turning. The hardness and surface roughness of the mold are obtained by heat treatment and surface chrome plating. In particular, the profile of the profile is irregular and asymmetrical, and the roller can easily scratch the surface of the aluminum profile. A nylon wheel can also be added between the steel mold and the aluminum profile to ensure the strength of the mold without directly contacting the aluminum profile with the steel mold to avoid scratching the surface of the material. An example of a typical roll bending workpiece is shown in Figures 10 and 11 .
(4) Calculation of roll forming ability
Whether the roll bending equipment meets the process requirements of the roll bending workpiece, the following conditions must be met:
1 Whether the length of the roller shaft satisfies the width dimension of the material. 2 Whether the minimum bending radius of the equipment roll is greater than the minimum arc of the workpiece. 3 Whether the equipment pressure is greater than the material roll forming force. The calculation of the roll forming force is the theoretical basis for verifying the roll bending ability of the roll bending equipment during the process evaluation process. The forming force calculation of the roll bending workpiece:
3. Press forming process
(1) Working principle of press forming The press forming process uses a hydraulic press to apply pressure to the material, and a bending moment is applied to the material by the bending die to bend the material to form a certain angle and curvature, as shown in Fig. 12.
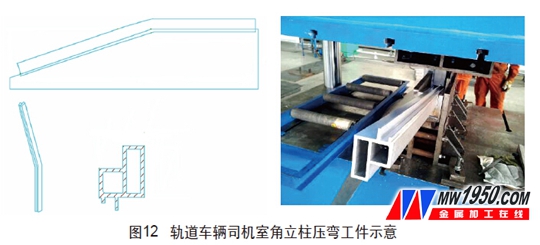
(2) Characteristics and key technology of press forming process The L-shaped and S-shaped bending parts of aluminum alloy profiles can be pressed and bent. Due to the different sections and shapes of the profiles, the design of the bending and bending of various bending and bending parts is different. In the same way, it is necessary to go through the continuous bending and bending process test to explore the rebound amount and obtain a reasonable mold pressing and bending surface after several times of repairing. Several key technical points of the bending and bending process: 1 The design of the bending and bending mold should fully consider the deformation trend and rebound amount of the material. 2 Since the aluminum alloy profile has a cavity hollow structure, reasonable filler selection is the key to compression forming. 3 For asymmetrical profiles with cross-section shapes, effective measures to prevent side bends should be fully considered during bending.
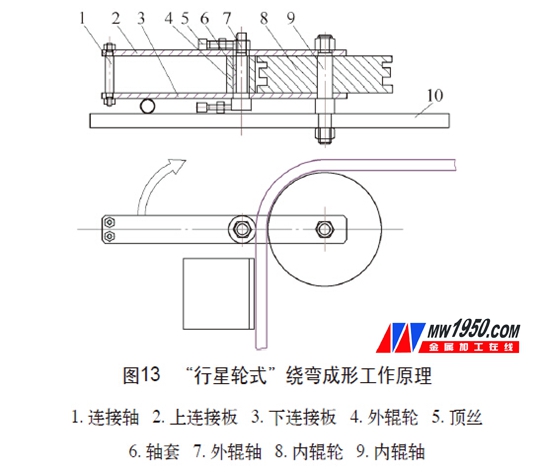
4. Winding forming process
(1) Working principle of winding forming The bending process is divided into two working modes: 1 mode 1: as shown in Fig. 13, the outer roller 4 rotates around the inner roller 8 and under the radial roller pressure of the inner and outer rollers The material is rolled and formed into a "planetary wheel". 2 Mode 2: As shown in FIG. 14, the material 1 is fixed on the bending die 2 by the clevis 3, and the bending die 2 is circularly moved to drive the material 1 to complete the bending under the action of the pressing die 5 and the guiding die 4.
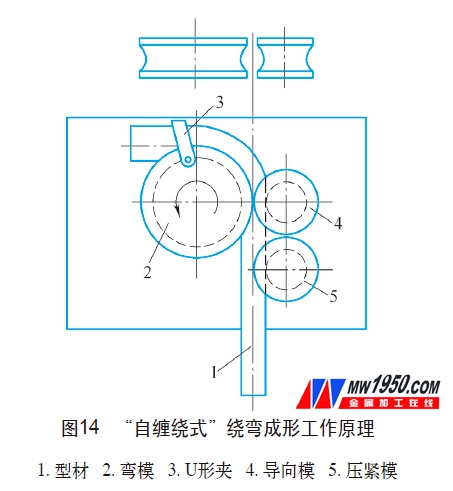
The difference between the two modes is that the mode 1 material does not move vertically, while the mode 2 material moves in the longitudinal direction with the bending mode, and the mode 2 can add the core block in the bending of the thin-walled profile to prevent the material from being deformed in section. The bending forming is widely used in the bending process of the profile, and the organic combination of the two bending modes can realize the realization of the complex multi-radial workpiece, as shown in Fig. 15 for the winding of the S-shaped workpiece.
5 Conclusion
The four arc bending processes introduced above are the most commonly used methods for arc bending of aluminum alloy profiles. In the actual process development, which process needs to be comprehensively analyzed according to the design and theoretical calculation of curved arc workpieces, Similar workpieces are compared in practice. In the early stage of the design of the mold or tooling, the problems that are expected to occur in the curved parts are listed. The analysis is carried out in combination with the various methods. When the tooling design is carried out, corresponding measures are taken to cope with the occurrences in the bending. problem. Profile bending is a comprehensive technology. The various arc bending principles need to be thoroughly penetrated, and the process designers need to continuously sum up experience and accumulate in the long run, in order to take effective and reasonable bending for various curved workpieces. Arc production plan.
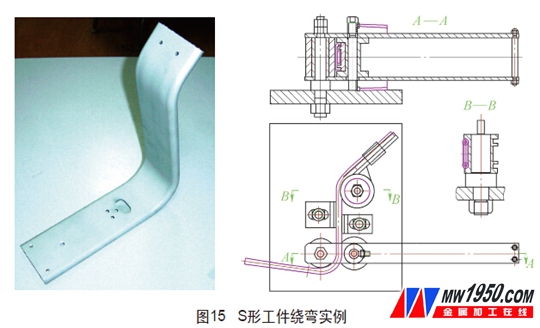
About the author: Yang Xingliang, Liaoning Zhongwang Group Co., Ltd. Aluminum alloy body manufacturing plant.
Wood Activated Carbon is a black powder, granular or pellet or amorphous with porous carbon. The main component is carbon, which also contains small amounts of oxygen, hydrogen, sulfur, nitrogen, and chlorine. It is mainly made of wood, fruit shells, coal and other high-temperature activation. Carbon is the most stable element in nature. Activated Carbon also has this feature. Activated carbon pore structure is advanced, with a large surface area (500 ~ 1000 m2/g), even higher, has a strong physical adsorption properties, can adsorb gas, liquid or colloidal solids; for gases, liquids, adsorbed substances The quality can be close to the quality of the activated carbon itself. Its adsorption is selective, non-polar substances are more easily adsorbed than polar substances. In the same series of substances, substances with higher boiling points are more easily adsorbed, and the pressure is higher, the temperature is lower, the concentration is greater, and the amount of adsorption is greater. Conversely, decompression and warming are favorable for desorption of gases.
Wood Activated Carbon
Wood Activated Carbon,Activated Charcoal,Charcoal Tablets,Activated Charcoal Tablets
NINGXIA SINOTOPSKY INTERNATIONAL TRADING CO.,LTD. , https://www.nxsinotopsky.com